





Pharma grade parts and glassware washers
DS PH – Pharma Grade Parts Washers are engineered and utilized for throughput, efficiency, and validatable cleaning and drying of various materials and components used in Biotechnology and Pharmaceutical Manufacturing processes, including laboratory glassware, filling line components, tools, tubing, TC fittings, valves and pump bodies, filter housings, reactor vessels, and miscellaneous equipment.
Washers can be configured for different layouts and workflow requirements: single door or double door pass-through versions; with automatic motorized opening, vertical or horizontal sliding doors. Available also in hinged door version, full glass or stainless steel, to reduce footprint and ensure easy and safe access. Available in a wide range of chamber sizes, from 230 to 2,400 litres, configurations and accessories to tailor each unit to the specific client requirements.
The design of the GMP range ensures self-cleaning of the chamber and pipework at each process stage, to prevent cross-contamination. Excellent cleaning and drying performance, combined with reduced process time and water consumption, characterize the DS series.
The heating elements, located in the sump, are pharma industry compliant, sanitary and dead leg free, fabricated from AISI 316L (1.4404) stainless steel and electro-polished. They may be connected to plant steam in the Steam heat exchanger version or directly to plant power in the Electrical heat exchanger version.
Steelco GMP washers are designed, manufactured, validated, and documented according to the latest global practices and standards to facilitate customer compliance with current Good Manufacturing Practices (cGMPs).
Cycle development pharma washer
Steelco pharma-grade washers can run different cycle recipes, selectable from the operator panel. Each recipe is a combination of the following phases with adjustable setpoints and durations:
- Pre-wash
- Wash with or without detergent(s)
- Rinse with or without recirculation
- Recirculated, single-pass, or sequential final rinse
- Drying
- Cooling
- In-between above steps, air purging of process piping is available to avoid any risk of cross-contamination
All standard or custom cycle recipes are analyzed and identified during the design phase, according to the items to be cleaned.
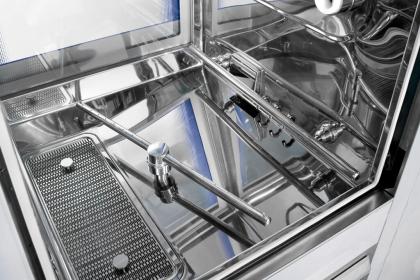
Reliable and hygienic construction
The washing chamber and the hydraulic system are designed and constructed with extreme care and have a surface finish with roughness average Ra<0.51 pm / 20pin (Ra<0.38 pm / 15pin available upon request). All wetted surfaces are crevice-free construction, with orbital welding for piping to eliminate water retention and stagnation points where biofilm could accumulate. AISI 316L stainless steel is used internally with EPDM, PTFE, or other FDA-approved (21CFR part 177) material gaskets. All models feature angled surfaces and rounded corners to ensure complete drainage. Detailed engineering on the sump reduces water consumption and assures high performance in terms of both cleaning and consumption. Multiple sanitary rotating washing arms are located on the top and on the bottom of the chamber to provide full washing and drying coverage for the items being processed, as well as the chamber.
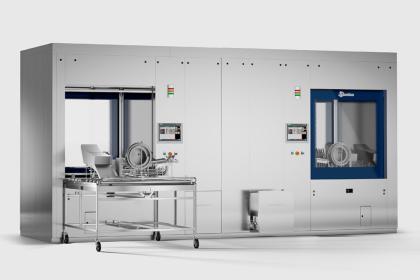
Complete layout versatility
DS Series can be configured with different layouts: single door or double door pass-through version, offering sliding and hinged door models in various configurations: with an automatic motorized (vertically or horizontally) opening, in high-visibility full glass, or in stainless steel. The electrical cabinet and the drying system can be integrated within the skid of the unit or remotely installed. The technical area can be on the right or left side; alternatively, it can be shared in the case of "inline" installation of a pair of machines.
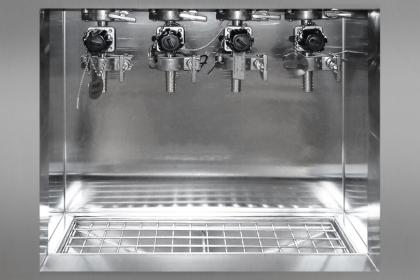
Effective sampling solutions
Sampling of process media is a key Quality Assurance requirement in any pharmaceutical cleaning process and cleaning validation procedure. Steelco offers a wide range of sampling systems to meet the most rigorous requirements:
- Water sampling from the sump
- Water sampling from final rinse system
- Water sampling from the point of use for each water
- Process compressed air line (PCA) sampling
- Clean steam sampling
For each sampling solution a TIC port, a manual or automatic valve can be installed in the technical service area or in an alcove on the machine fascia panel, according to client requirements.
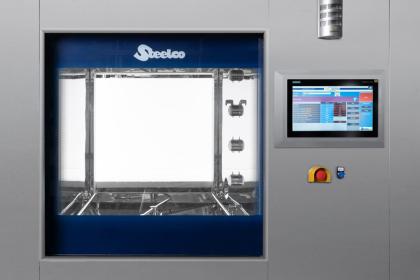
Integrated automation architectures
Steelco provides a range of user-friendly control systems developed according to the latest ISPE GAMP(c) Guidelines and designed for FDA 21 CFR Part 11 and EU Annex 11 compliance. System platforms available include Siemens or Rockwell/Allen-Bradley. Irrespective of the platform, all Steelco Pharma equipment (washers, autoclaves, etc) has a common look and feel, consistent interface, and common GMP data management. Four levels are available, ranging from a local, standalone system to being fully integrated with the client IS infrastructure, in which the machine SCADA and related databases are hosted on the client network, providing the highest levels of data integrity and allowing in-house IT support and maintenance. Dependent on client policy, Steelco offers remote access via a virtual private network (VPN) to provide support during start-up, qualification, and maintenance activities.
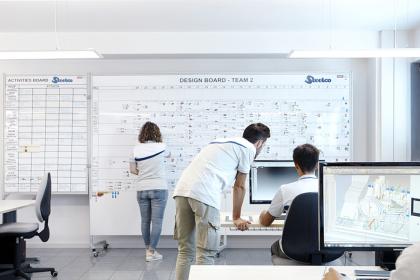
Quality engineering process and qualification services
Technical consulting, design, engineering, project management, as well as commissioning and qualification services of our equipment are offered, with customers appreciating the cost-effective, high-performance solutions offered to resolve complex washing and sterilization challenges. Design Qualification (DO), Installation Qualification (IQ), Operational Qualification (OQ), and Performance Qualification (PQ) are provided with standard or customized protocols according to the final scope of supply. Customers are always welcome to visit Steelco factories to see design and manufacturing methods and audit our processes. Steelco Group is available anytime to support customers during all acceptance on-site including process and cycle development.
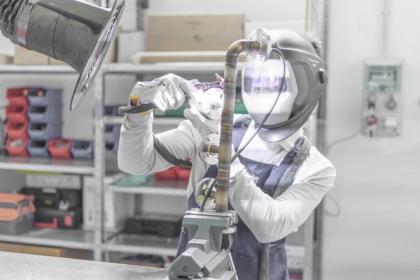
Customized rack configurations
Steelco designs, develops, manufactures, and tests its own racks and trolleys in-house, ensuring that this critical process' quality attribute is assured and providing a single point of responsibility for the design and function of the entire cleaning process. Steelco's engineering experience and sophisticated 3D CAD programs provide that every point, corner, and cavity of an item to be processed is deeply and efficiently cleaned, thus avoiding the possibility of cross-contamination and eliminating all soil and contaminant residues from the previous process. The same injection porting is used to also convey hot sterile filtered air inside each cavity for effective drying.